Budowa maszyn przemysłowych na zamówienie to proces, który wymaga starannego planowania oraz realizacji. Kluczowym etapem…
Budowa maszyn pneumatycznych opiera się na kilku kluczowych elementach, które współdziałają ze sobą, aby zapewnić efektywne działanie systemu. Przede wszystkim, podstawowym komponentem jest sprężarka, która odpowiada za generowanie sprężonego powietrza. Sprężarki mogą być różnego rodzaju, w tym tłokowe, śrubowe czy wirnikowe, a ich wybór zależy od specyficznych potrzeb aplikacji. Kolejnym istotnym elementem są zbiorniki powietrza, które magazynują sprężone powietrze i umożliwiają jego równomierne dostarczanie do pozostałych części systemu. W układzie pneumatycznym niezbędne są również zawory sterujące, które regulują przepływ powietrza oraz ciśnienie w systemie. Zawory te mogą być ręczne lub automatyczne, a ich odpowiedni dobór ma kluczowe znaczenie dla wydajności całego układu. Dodatkowo, w budowie maszyn pneumatycznych wykorzystuje się siłowniki pneumatyczne, które przekształcają energię sprężonego powietrza w ruch mechaniczny. Siłowniki te mogą mieć różne konstrukcje i parametry techniczne, co pozwala na ich zastosowanie w różnych branżach przemysłowych. Ostatnim istotnym elementem są przewody pneumatyczne, które łączą wszystkie komponenty i umożliwiają transport sprężonego powietrza.
Jakie są zalety i wady budowy maszyn pneumatycznych
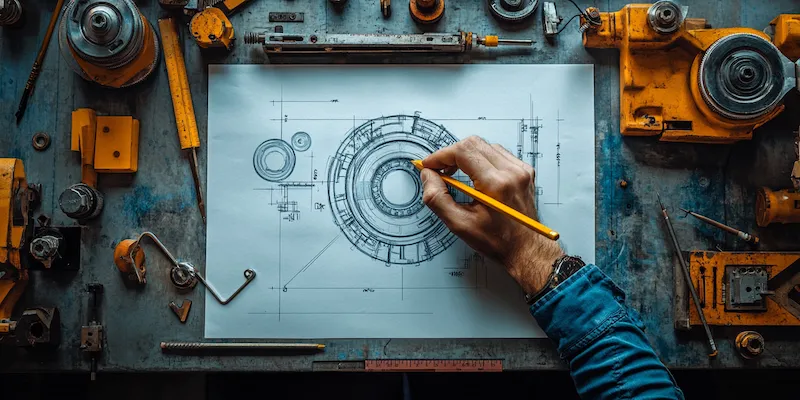
Budowa maszyn pneumatycznych niesie ze sobą wiele zalet oraz pewne wady, które warto rozważyć przed podjęciem decyzji o ich zastosowaniu. Do głównych zalet należy zaliczyć prostotę konstrukcji oraz łatwość w eksploatacji. Systemy pneumatyczne są zazwyczaj mniej skomplikowane niż hydrauliczne czy elektryczne, co przekłada się na niższe koszty utrzymania oraz łatwiejszą konserwację. Ponadto maszyny pneumatyczne charakteryzują się dużą prędkością działania oraz możliwością pracy w trudnych warunkach atmosferycznych. Sprężone powietrze jest także bezpieczniejsze od innych mediów roboczych, ponieważ nie stwarza ryzyka wybuchu ani zanieczyszczenia środowiska. Niemniej jednak budowa maszyn pneumatycznych ma również swoje wady. Jedną z nich jest ograniczona moc i wydajność w porównaniu do systemów hydraulicznych, co może być problematyczne w przypadku bardziej wymagających aplikacji. Dodatkowo sprężone powietrze ma tendencję do rozprężania się, co może prowadzić do strat energii i obniżenia efektywności całego systemu.
Jakie są zastosowania budowy maszyn pneumatycznych w przemyśle
Maszyny pneumatyczne znajdują szerokie zastosowanie w różnych gałęziach przemysłu ze względu na swoją wszechstronność oraz efektywność działania. W przemyśle produkcyjnym wykorzystuje się je do automatyzacji procesów montażowych oraz pakowania produktów. Dzięki zastosowaniu siłowników pneumatycznych możliwe jest szybkie i precyzyjne wykonywanie operacji takich jak chwytanie, przenoszenie czy składanie elementów. W branży spożywczej maszyny pneumatyczne służą do transportu surowców oraz pakowania gotowych produktów, co przyczynia się do zwiększenia wydajności linii produkcyjnych. Kolejnym obszarem zastosowań są systemy transportu wewnętrznego, gdzie sprężone powietrze wykorzystywane jest do napędu różnego rodzaju taśmociągów oraz urządzeń transportowych. W przemyśle motoryzacyjnym maszyny pneumatyczne odgrywają kluczową rolę w procesach lakierniczych oraz montażowych, gdzie precyzyjne sterowanie ruchem jest niezbędne dla uzyskania wysokiej jakości produktów końcowych. Ponadto technologie pneumatyczne znajdują zastosowanie w robotyce przemysłowej, gdzie umożliwiają tworzenie elastycznych i wydajnych systemów produkcyjnych.
Jakie nowoczesne technologie wspierają budowę maszyn pneumatycznych
Nowoczesne technologie znacząco wpływają na rozwój budowy maszyn pneumatycznych, wprowadzając innowacyjne rozwiązania poprawiające ich wydajność oraz funkcjonalność. Przykładem takiej technologii jest Internet Rzeczy (IoT), który pozwala na zdalne monitorowanie i zarządzanie systemami pneumatycznymi. Dzięki czujnikom umieszczonym w różnych częściach układu możliwe jest zbieranie danych dotyczących ciśnienia, temperatury czy przepływu powietrza, co umożliwia optymalizację pracy maszyn oraz szybsze wykrywanie ewentualnych usterek. Kolejnym kierunkiem rozwoju są inteligentne zawory sterujące, które dzięki zaawansowanym algorytmom potrafią automatycznie dostosowywać parametry pracy układu do zmieniających się warunków produkcji. Wprowadzenie technologii sztucznej inteligencji pozwala na lepsze prognozowanie awarii oraz planowanie konserwacji maszyn, co przekłada się na zwiększenie efektywności całego procesu produkcyjnego. Dodatkowo rozwój materiałów kompozytowych i lekkich stopów metali przyczynia się do zmniejszenia masy komponentów maszyn pneumatycznych, co z kolei wpływa na ich mobilność i łatwość w instalacji.
Jakie są kluczowe wyzwania w budowie maszyn pneumatycznych
Budowa maszyn pneumatycznych wiąże się z różnymi wyzwaniami, które mogą wpływać na ich efektywność oraz niezawodność. Jednym z głównych problemów jest zarządzanie sprężonym powietrzem, które jest medium roboczym w tych systemach. Utrzymanie odpowiedniego ciśnienia oraz jakości sprężonego powietrza jest kluczowe dla prawidłowego działania maszyn. Zanieczyszczenia, takie jak woda, olej czy cząstki stałe, mogą prowadzić do uszkodzeń komponentów oraz obniżenia wydajności. Dlatego konieczne jest stosowanie odpowiednich filtrów oraz osuszaczy powietrza, co generuje dodatkowe koszty i wymaga regularnej konserwacji. Kolejnym wyzwaniem jest zapewnienie odpowiedniej synchronizacji pracy różnych elementów systemu. W przypadku skomplikowanych układów pneumatycznych, gdzie wiele siłowników działa jednocześnie, precyzyjne sterowanie staje się kluczowe dla uniknięcia kolizji oraz zapewnienia płynności procesów. Warto również zwrócić uwagę na kwestie związane z hałasem generowanym przez sprężarki oraz inne komponenty pneumatyczne. Wysoki poziom hałasu może negatywnie wpływać na komfort pracy operatorów oraz wymagać dodatkowych rozwiązań akustycznych.
Jakie są przyszłościowe kierunki rozwoju budowy maszyn pneumatycznych
Przyszłość budowy maszyn pneumatycznych zapowiada się obiecująco, a rozwój technologii otwiera nowe możliwości dla tego segmentu przemysłu. Jednym z kluczowych kierunków rozwoju jest automatyzacja procesów produkcyjnych, która staje się coraz bardziej powszechna w różnych branżach. Wprowadzenie robotyzacji oraz sztucznej inteligencji do systemów pneumatycznych pozwala na zwiększenie wydajności oraz elastyczności produkcji. Dzięki zastosowaniu zaawansowanych algorytmów możliwe jest optymalizowanie pracy maszyn w czasie rzeczywistym, co przekłada się na oszczędności energii oraz surowców. Innym istotnym trendem jest rozwój technologii zdalnego monitorowania i diagnostyki, które umożliwiają bieżące śledzenie stanu maszyn i szybką reakcję na ewentualne awarie. Systemy te wykorzystują czujniki i urządzenia IoT do zbierania danych o pracy maszyn, co pozwala na lepsze planowanie konserwacji oraz minimalizację przestojów. Dodatkowo rosnące zainteresowanie ekologicznymi rozwiązaniami sprawia, że producenci maszyn pneumatycznych poszukują sposobów na zmniejszenie zużycia energii oraz emisji hałasu. Wprowadzenie bardziej efektywnych sprężarek oraz materiałów o niskim oporze przepływu powietrza może przyczynić się do poprawy efektywności energetycznej całego systemu.
Jakie są różnice między budową maszyn pneumatycznych a hydraulicznymi
Budowa maszyn pneumatycznych różni się od hydraulicznych pod wieloma względami, co ma istotny wpływ na ich zastosowanie w różnych branżach przemysłowych. Przede wszystkim podstawową różnicą jest medium robocze – maszyny pneumatyczne wykorzystują sprężone powietrze, podczas gdy maszyny hydrauliczne działają na zasadzie cieczy hydraulicznej. To sprawia, że maszyny pneumatyczne są zazwyczaj lżejsze i prostsze w konstrukcji niż ich hydrauliczne odpowiedniki, co przekłada się na łatwiejszą instalację i konserwację. Ponadto sprężone powietrze jest bardziej bezpieczne w użyciu niż ciecz hydrauliczna, która może być toksyczna lub łatwopalna. Z drugiej strony maszyny hydrauliczne oferują większą moc i precyzję działania, co czyni je bardziej odpowiednimi do zastosowań wymagających dużych sił, takich jak prasy czy maszyny budowlane. W kontekście kosztów eksploatacji warto zauważyć, że systemy pneumatyczne mogą generować mniejsze koszty utrzymania ze względu na prostszą konstrukcję i mniejsze ryzyko awarii. Jednakże w przypadku aplikacji wymagających dużej mocy hydraulika może okazać się bardziej opłacalna ze względu na swoją wydajność.
Jakie są najczęstsze błędy przy budowie maszyn pneumatycznych
Podczas budowy maszyn pneumatycznych często popełniane są błędy, które mogą prowadzić do obniżenia efektywności działania systemu lub nawet jego awarii. Jednym z najczęstszych błędów jest niewłaściwy dobór komponentów do konkretnej aplikacji. Zastosowanie niewłaściwej sprężarki lub siłownika może skutkować nieoptymalnym działaniem całego układu oraz zwiększeniem kosztów eksploatacji. Ważne jest także uwzględnienie parametrów technicznych takich jak ciśnienie robocze czy wydajność powietrza przy wyborze elementów systemu. Kolejnym powszechnym błędem jest niedostateczna konserwacja urządzeń pneumatycznych. Regularne czyszczenie filtrów powietrza oraz kontrola stanu technicznego sprężarek są kluczowe dla zapewnienia długotrwałego działania maszyn i uniknięcia nieprzewidzianych przestojów. Niezbędne jest również dbanie o jakość sprężonego powietrza poprzez stosowanie odpowiednich filtrów i osuszaczy, aby zapobiec uszkodzeniom komponentów układu. Inny błąd to niewłaściwe rozmieszczenie przewodów pneumatycznych, które może prowadzić do strat ciśnienia oraz obniżenia wydajności systemu.
Jakie są najlepsze praktyki w budowie maszyn pneumatycznych
Aby zapewnić efektywność i niezawodność budowy maszyn pneumatycznych warto stosować najlepsze praktyki w zakresie projektowania i eksploatacji tych systemów. Kluczowym krokiem jest dokładne zaplanowanie projektu już na etapie koncepcji, uwzględniając wszystkie wymagania techniczne oraz specyfikacje aplikacji. Ważne jest również przeprowadzenie analizy ryzyka przed rozpoczęciem budowy, aby zidentyfikować potencjalne problemy i opracować strategie ich minimalizacji. Dobór wysokiej jakości komponentów to kolejny istotny element – warto inwestować w sprawdzonych producentów oraz materiały o wysokich parametrach technicznych. Regularna konserwacja urządzeń to niezbędny krok w utrzymaniu ich sprawności; zaleca się opracowanie harmonogramu przeglądów technicznych oraz bieżącego monitorowania stanu układów pneumatycznych za pomocą czujników i systemów diagnostycznych. Szkolenie personelu obsługującego maszyny również ma kluczowe znaczenie – dobrze przeszkoleni pracownicy będą w stanie szybko reagować na ewentualne problemy oraz podejmować właściwe decyzje operacyjne.